こんにちは!人事の山本です。
今回は、2019年12月にホワイトプラスに入社し、『リネット』の中核を担っている、品質・生産管理グループのマネージャー中山さんに、グループのミッションや業務内容、今後お客様にどんな価値を届けたいのかお話を聞きました。
「仕事の幅を広げてビジネスを楽しみたい」という思いからホワイトプラスへ
--最初に、これまでのキャリアのお話を聞かせてください。
新卒で入社した会社でハード系のエンジニアを経験し、それからソフトウェアの開発エンジニアに転職しました。そのあと、前職である大手ECの生産管理部門に入社しました。
生産管理での転職は畑違いでしたが、ほとんど不安はなく、「いっちょ挑戦してやるか!」ぐらいの気持ちでしたね(笑)。
そこから生産管理の仕事が面白くなり、あっという間に惹き込まれていきました。
--そこからホワイトプラスに入社した理由を教えてください。
前職の会社が大きな組織で、業務がある程度縦割りになっていて、横断的に携わることができない構造にもどかしさを感じていました。もう少し業務の幅を広げて、ビジネス全体として楽しみたいという気持ちが強かったんですよね。
ホワイトプラスではすべての部門が自社内で内製されていて、経営層と近い距離で働くことができるという部分が魅力でした。
また、福利厚生が充実していて、ワークライフバランスを取っていける環境も決め手のひとつでしたね。
詳しくはこちらのインタビューをご覧ください。【社員インタビュー#7 生産管理・中山剛次】チャレンジしたいことも働き方も大切にしたかったからホワイトプラス以外は考えなかった
データを元にお客様満足度の向上を追求
--ホワイトプラスには「新しい日常をつくる」というビジョンがありますが、その中での品質・生産管理グループとしてのミッションを教えてください。
“繁忙期でも安定した品質を維持する”というミッションがあります。
お客様から再仕上を依頼された件数を、事故の件数として数え、事故率という表現をしています。その中で私が行なっている業務の一つが、事故率の改善になります。
--事故率を改善して、お客様の満足度を上げるということですね。具体的にはどういったことで改善を行なっていますか?
以前は、春先に向けての衣替えの時期に事故率が上がる傾向にありました。
そしてその原因が、繁忙期で衣類1点ごとにかける時間が少なくなっているからではないかという仮説があったんです。
繁忙期になるとコートやセーター類の受注の比率が非常に高くなり、結果として事故率が上がるということがわかりました。
そこで、事故率の高い衣類に対して集中的に改善を進めるアクションを決めて、検品とダブルチェックをより精度をあげていくことにたどり着きました。衣類によって見逃しやすいポイントが異なるので、衣類ごとに分解して、それを定量的に検品率という指標で追っています。
検品とダブルチェックというのは、一番の上流工程と下流工程、入り口と出口です。そこをしっかり固めることが、生産管理として一番効率的だと考えました。
提携するクリーニング生産パートナーとも、実際のデータを元にコミュニケーションを取ることで、改善のための具体的なアクションに繋げています。
この取り組みを2020年の春はこれまで以上に強化し、実際に事故率はかなり下がりました。
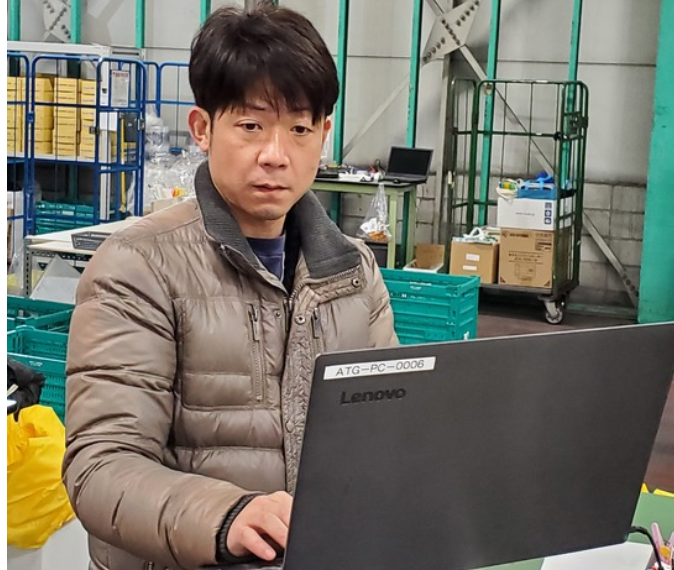
お客様の「声なき声」に耳を傾ける
--今後は、どのようなことに挑戦していきたいですか?
これまでお客様の声から不満をなくす活動を中心に行ってきましたが、今後は、お客様が心の中で思っているけど言葉には表していない、または気づいていない、いわゆる「声なき声」に耳を傾けて、それを満足度につなげていくといったアプローチもしていきたいです。
もしかしたらお客様は、こういうことを思っているかも?といった仮説を元に、お客様の満足や価値をもっと創造していくことができるのではないかと、部署内で日々議論しています。
具体的には、現在は「感動品質プロジェクト」に取り組んでいます。
科学的根拠に基づき、クリーニングの品質改善の再現性を上げることで、お客様アンケートの5段階のうちの最高評価の比率を上げるというプロジェクトです。
IT企業の強みを活かし、徹底的に数字で分析し、お客様に最高の品質をお届けできるようにチームのメンバーと取り組んでいます。
今までのクリーニングにはないものをお客様に提供し、感動を与えたいですね。
--品質改善の面白さや、やりがいを感じるところを教えてください。
私たちのサービスは対面販売ではないので、直接お客様の声が聞けるのはアンケートです。純粋にポジティブなコメントを頂くと嬉しいですし、それが私のモチベーションになっています。
提携する生産パートナーとは、毎月1回は定例ミーティングを開いて、どういった事故が多くなっているのか、どういったところを改善できているのかを話し合っています。
それ以外にも、定期的に各生産パートナーを訪問して、都度、品質改善を行います。そこでもお客様からの声を伝えて共有するのですが、もちろんネガティブな声もあります。しかし、そこで一緒に協力しながら品質改善に取り組めることにも、やりがいを感じますね。
--品質・生産管理グループの課題を教えてください。
クリーニングに出されるものは、素材や色・サイズだけではなく、お客様が着用されていた状態も違うので、同じ衣類はひとつもありません。そこで、かなり細分化された管理が必要になります。
一方で、やみくもに多くの時間を使って品質管理をするのでは、お客様に安い料金でサービスを提供できなくなってしまう恐れがあります。
そこのギャップを踏まえて、いかに効率的に、効果的に品質を改善していくかというところに難しさがあります。
--ホワイトプラスの3つのバリューを意識されている部分や、仕事を進める上での自分なりのルールを教えてください。
私は「のびしろで戦う~White Space~」が好きで、意識しているところです。
入社してまもなく1年になりますが、自分の強みは、ホワイトプラスやリネット生産開発部の中で今まで当たり前だったことに対して、新しい視点で切り込んでいけるところだと思うんですよね。
その強みを生かして貢献していきたいと思っています。
また個人的には、仕事を進める上で、社内外問わず「できない」という言葉は絶対に言わないようにしてます。どんなに難しいことがあっても、「できない」ではなく「できる」方法を模索していきたいと思っています。
中山 剛次(なかやま こうじ)
グロービス経営大学院 経営研究科 経営専攻 修了。電機メーカーや化粧品会社にて11年間エンジニアとして勤務した後、Amazonの入荷部門において生産管理業務に携わる。2019年12月ホワイトプラスに入社し、2020年8月より品質生産管理グループマネージャーを務める。